"Inspired by," "made from," "in tribute to": the watchmaking world is full of lexical tricks to describe copying processes. They draw their design from a given universe, but technically have no link to it. Among the most prominent industries: aviation, automobiles, where the less scrupulous skillfully blur the line between "real" and "plausible."
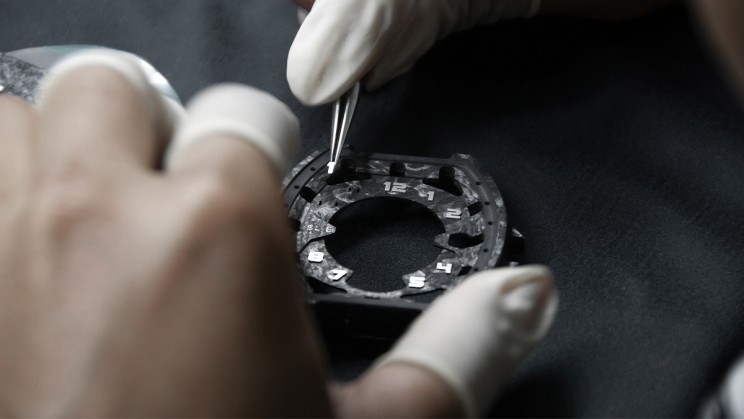
Pioneers
Historically, the credit goes to Yvan Arpa (ArtyA) for being the first, 20 years ago, to offer pieces with genuine fragments from the Titanic. The (now-defunct) RJ - Romain Jerome brand followed with its "DNA" series. Even HYT joined in, with a limited series enriched with sand from St. Barth. But no brand had accomplished what Lorige managed to do: a watch case 100% machined from brake pads of race-winning cars on some of the world’s greatest circuits.
Quiet on set
Technically, the process requires heavy development. Nearly three years for Lorige. But its three partners were not watchmakers, nor expected at trade shows, and even less so for large series production. This allowed them to work quietly until they achieved a perfect result.
The result is difficult to achieve because race car brake pads undergo intense stress. Under heavy braking, the carbon reaches 900°C. This temperature melts the resin that acts as a binder between the carbon particles. The material becomes porous, which is contradictory to the creation of a watch case, which, by definition, must remain watertight.
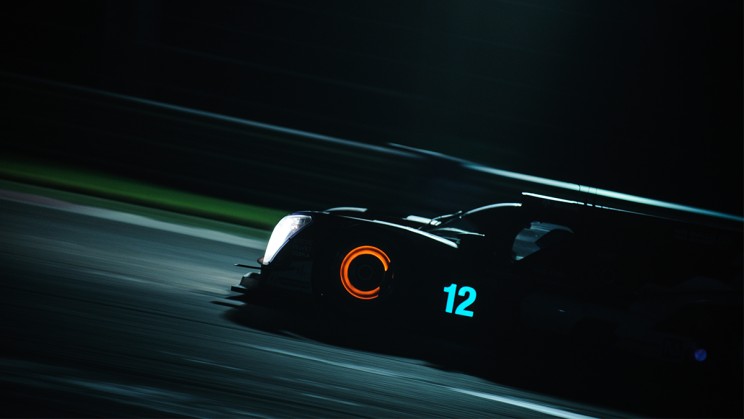
Double Machining
The challenge was to recover carbon brake pads, perform a first machining of two cases within each pad, inject resin again, and then repeat the entire process a second time to perfect it. This operation is followed by five hours of manual labor to achieve flawless surface finishes.
Along the way, Lorige developed two unique skills. The first: using the resin to fill the pores of its carbon cases. It was necessary to find an ultra-fluid material capable of infiltrating every nook and cranny of the material and then penetrating all the way through the depth of the carbon block. "It’s a resin we identified in the wind turbine blade industry," says Clément Etienvre, co-founder of Lorige.
The second development: achieving smooth surfaces. Carbon is naturally resistant to this. Lorige bypassed the issue by machining each case on two levels, separated by 0.1 to 0.2 millimeters. The higher level, which comes into contact with the watch's case components (bezel, crown, case back, etc.), is injected with resin, making it solid and perfectly smooth. The lower level has a different fiber geometry, more technical and closer to the original brake pad.
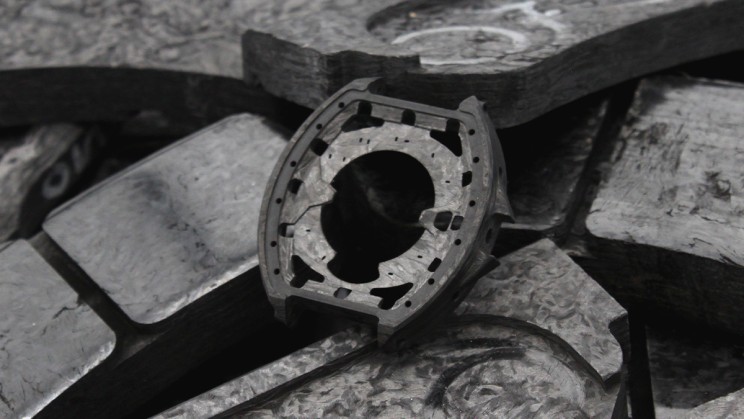
Unique Pieces
It takes 30 hours to machine one case. Quantities remain very limited. "We can only make one or two cases per pad. If we buy 8 pads, with slight wastage, we’ll get 15 cases, no more. We can’t restart. The original pad, whose entire history on the track is documented, will be completely used up," concludes Clément Etienvre.