Undertaken in 2019 by Chronométrie Ferdinand Berthoud, the Naissance d'une Montre 3 project is nearing its conclusion.
The first in this series of 11 fusee-and-chain timepieces, entirely produced without digital assistance, will be unveiled in the second half of 2025.
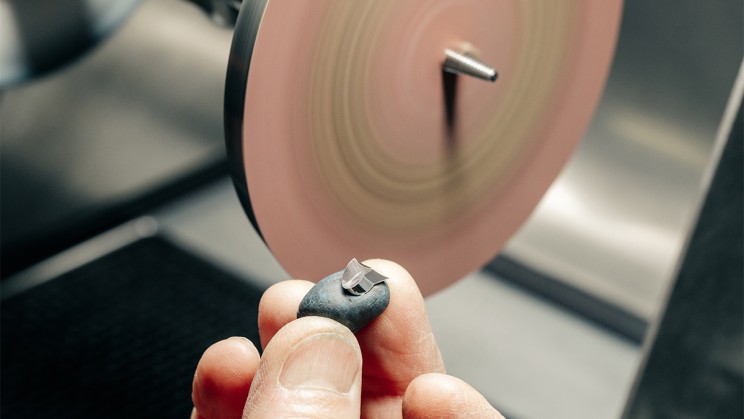
In the run-up to this official launch, one final aesthetic aspect of the project is being revealed: the watch exterior, crafted using traditional production methods.
These days, watch exterior components such as the case, bezel, lugs, crown or buckle are designed using computer-assisted design (CAD). Their plans and dimensions are then transferred to numerically controlled (CNC) equipment that machines them from the chosen material.
This process ensures perfect continuity between the design and the final result, working within infinitely small tolerances. However, when the decision is taken – as it was for the Naissance d'une Montre project – to do away with all digital assistance, challenges re-emerge from the historical depths of traditional watchmaking. Challenges that must be resolved by hand, on conventional machines equipped with a single tool.
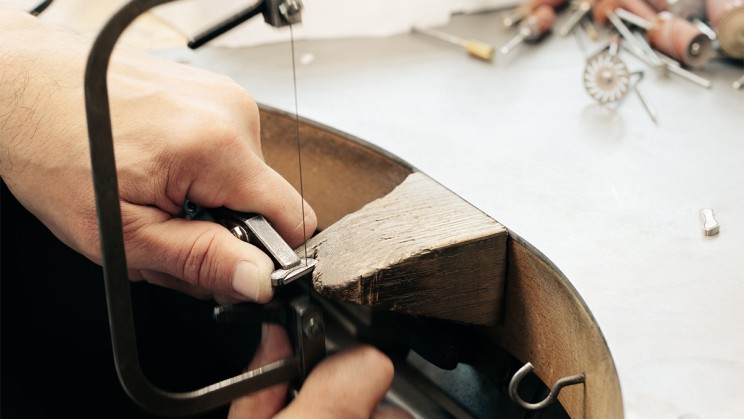
Production of the exterior components for the Naissance d'une Montre 3 timepiece was no exception to this ‘back to basics’ approach. They include a curved case middle and bezel, applied lugs as well as a crown and buckle featuring complex shapes. Inspired by the work of Ferdinand Berthoud, these singular geometrical forms are particularly tricky to achieve using hand-operated machine tools.
To overcome this stumbling block, Chronométrie Ferdinand Berthoud opted to engage in broader collaboration within the Chopard group. Processes such as lost-wax casting originating from the jewellery industry; as well as turning, milling and tapping which are typically micromechanical procedures, made it possible to leverage in-house expertise to the full in producing the most complex shapes.
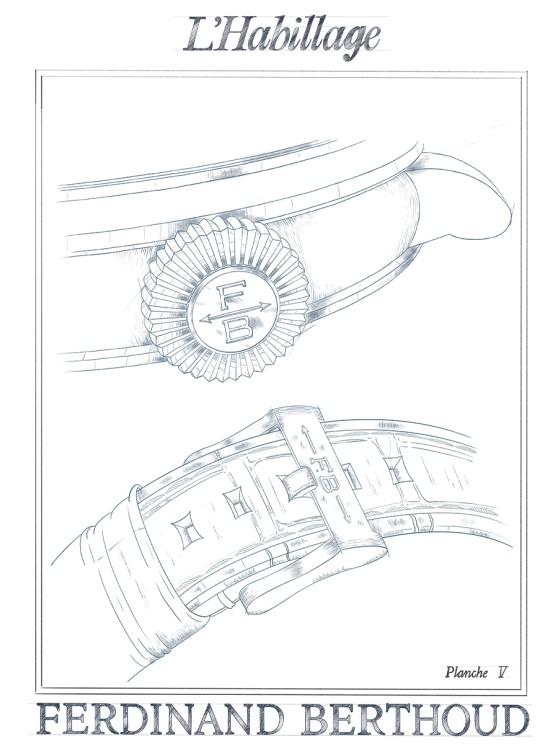
Once the final form has been obtained, manual finishing crafts take over once again: reworking the blank, trimming and polishing. Certain elements such as the lugs are then welded, prior to manual decoration (engravings and hallmarks).
This collaborative approach is the very essence of Naissance d’une Montre 3. Nearly 70 employees from Chopard and Ferdinand Berthoud were involved in this project aimed at transmitting and safeguarding traditional watchmaking expertise.